Frostbite
Novel Cold-Therapy Device For Post Surgery Recovery
Role
Build Studio Engineer
Timeframe
January-May 2018
Skills
Experimental Design
CAD/Rendering
3D printing
Thermal systems analysis
I joined Generate as a second year student and it opened my eyes to the world of product development and entrepreneurial engineering. I joined initially as a build studio engineer and immediately got hands on experience on early stage development of an innovative cold therapy device for post-orthopedic surgery Frostbite. This was my first exposure to working on a truly integrated interdisciplinary team working closely with chemical, mechanical, and electrical engineers to deliver both a “works-like” prototype of the device alongside a “looks-like” rendering. As a younger member on the team I had little knowledge of some of the thermodynamic intricacies of the device and was mostly responsible for designing and running tests on our prototypes as well as defining success criteria beyond what was listed in our original scope document
The Product
After orthopedic surgery, patients often need to continue to ice the surgical site after leaving the hospital to reduce swelling and ease healing
Existing solutions involve a typical beach cooler filled with ice and a pump that circulates the cold water through a cooling pad of sorts.
This solution requires patients in recovery to not only transport a heavy cooler anytime they need to change positions but to refill and stock heavy ice bags
This is especially a problem for patients with arm and shoulder injuries who cannot lift heavy weights
The client proposed using a self contained device that circulated and cooled water when plugged in to the wall in hopes of making the device compact and requiring patients to do less work while under cold therapy
We were asked to explore this field and build a functional prototype that would demonstrate the feasibility of our technology, as well as a scaled down experiential prototype
Design Process
System illustration diagram that shows the use of Peltier thermoelectric devices to transfer heat from the water out through the heat sink
The team began by considering a variety of different cyclic refrigeration technologies, namely vapor-compression and thermoelectric systems.
The team quickly determined that Vapor compression would involve too much complexity and add weight to the devices
Thermoelectric coolers combined with heat exchangers on the other hand enable us to create a very compact and space efficient device
Thermoelectric coolers are an interesting technology that makes use of the differences in charge of a material when an electric current is passed through them.
When a current is applied thermal energy will move across the device against the thermal gradient
Based on the specifications of the device there will be a constant temperature delta maintained across the two sides. The devices become less efficient as more heat is transferred through it
In our design the device acts like a heat pump, absorbing heat energy from the water and transferring it against the thermal gradient to the hot side of the device where it is exhausted via a heat sink and forced convection.
After initial research and selecting the thermoelectric system we created system diagram to chart the flow and cooling process
At this stage the team also tested competitor devices and worked to define numerical specifications for a target weight and size for the device, as well as electrical power specifications and a target therapeutic temperature of 17ºC
We then performed thermodynamic analysis on system to determine the system’s thermal load and spec a thermoelectric device and heatsinks that met our needs
The team then worked with vendors to purchase the thermoelectric device and assembled the rest of the system (heat exchangers, heatsinks, fans, and pump) using COTS parts
We then extensively tested the prototype, first to see if it could reach the target temperature as designed, and then seeing exactly how long it would take to cool down, and how long it could hold the target temperature
Finally the team designed and 3D printed scale prototype of device to demonstrate the design and packaging of a potential final product that used the same system architecture.
The design also added some features including ducting between the fans and heatsink to maximize airflow and minimize heat loss
Challenges
Chiefly, to cool to lower temperatures in the therapeutic range, we needed the heatsinks and fans placed above the device have to be able to extract as much heat as possible with little thermal loss between the device and the heat sinks above.
Solving this problem beyond using thermal paste proved difficult as we experimented with other thermal transfer materials that could conduct the heat effectively between the two.
Eventually the team landed on a copper strip placed on the hot side of the heatsink to bridge the transfer of the two devices into a bank of 3 heat sinks. This combined with forced convection from 2 computer fans allowed us to go below our target temperature and as low as 14ºC
The other major challenge we faced was on the electrical side. To cool effectively, the thermoelectric devices required a big power draw. Though this was a known challenge before embarking on the design of the board, the difficulty of running such high power through a PCB proved to be one of our most pressing challenges.
A stopgap solution was put in place with a small bit of firmware that modulated the power supplied to the thermoelectric devices to prevent board components from overheating. This was sufficient for the purposes of the project but would be unacceptable as a long term solution and harmed the efficacy of the device in operating conditions.
Final Product
Over the course of the semester Generate performed research and development on an early stage prototype for a novel post-surgery cold therapy device that provided portability and convenience to patients. The device made use of thermoelectric coolers to cool a water circuit. A pump is used to circulate the water between the cooling blocks affixed to the Peltier devices and the therapy pad that is applied to the patient. Heat sinks and fans were used to remove excess heat from the hot side of the peltier device. The system will be integrated into a sleek outer-housing designed to optimize airflow and minimize overall size and weight. In terms of performance the device was able to effectively and repeatedly cool the pad to a therapeutic temperature of 17ºC and in optimal conditions reach temperatures as low as 14ºC. The client was satisfied with our work and will continue to develop the product.
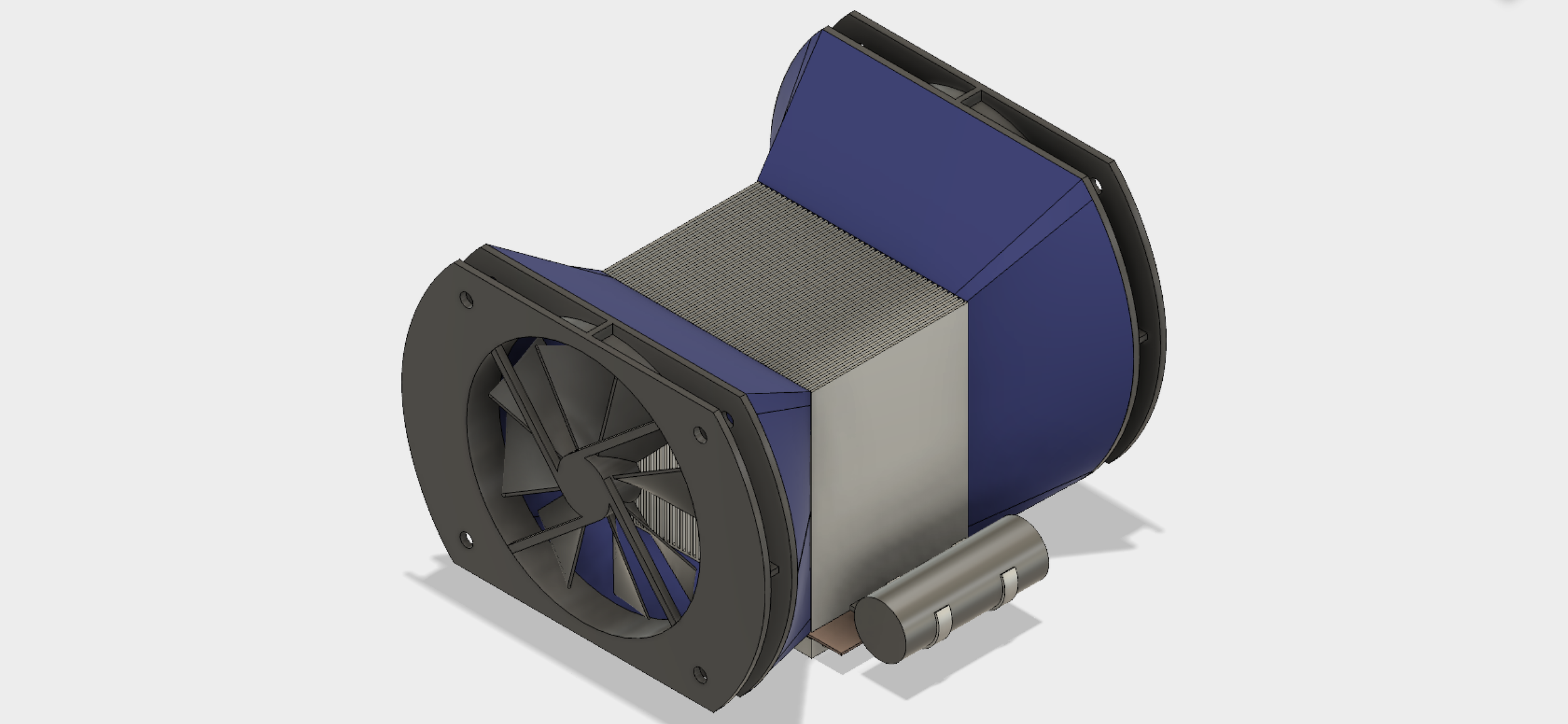

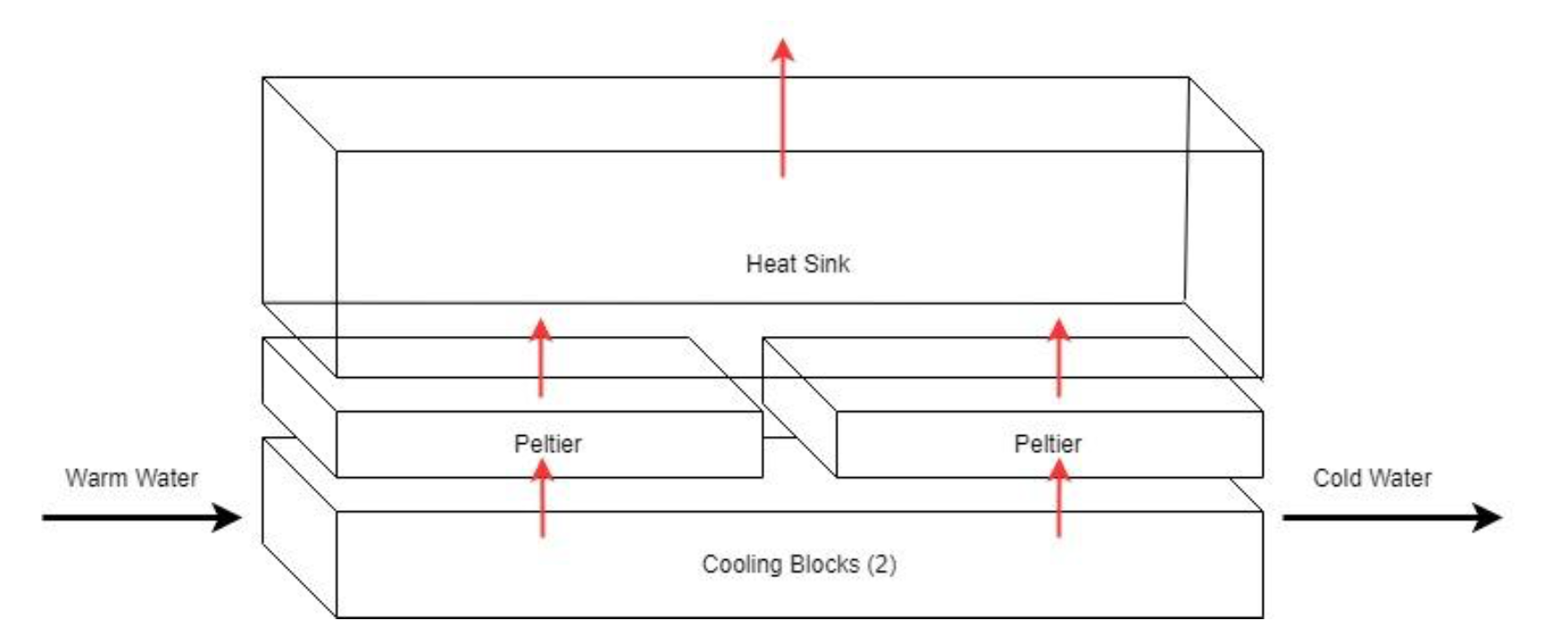
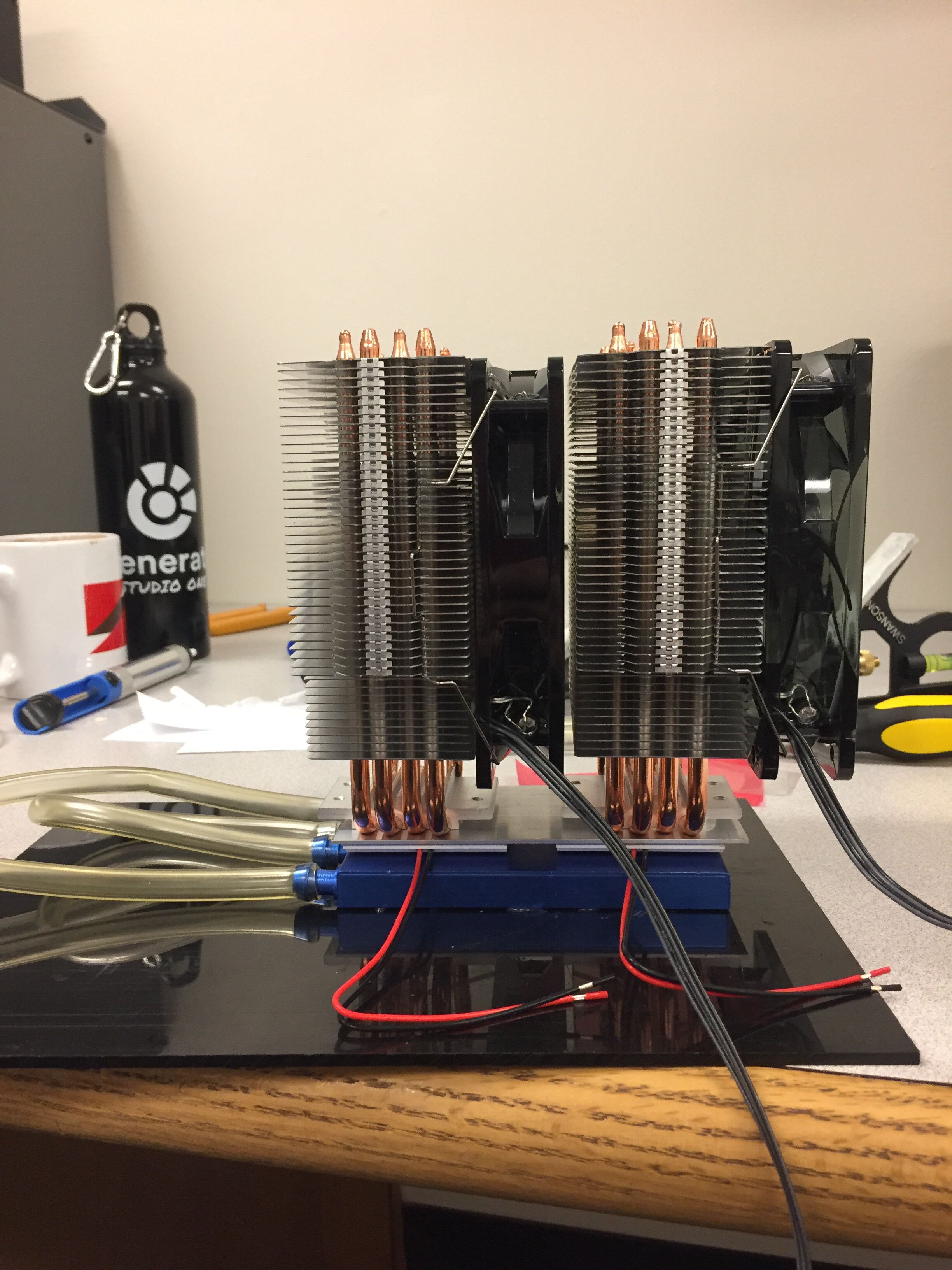
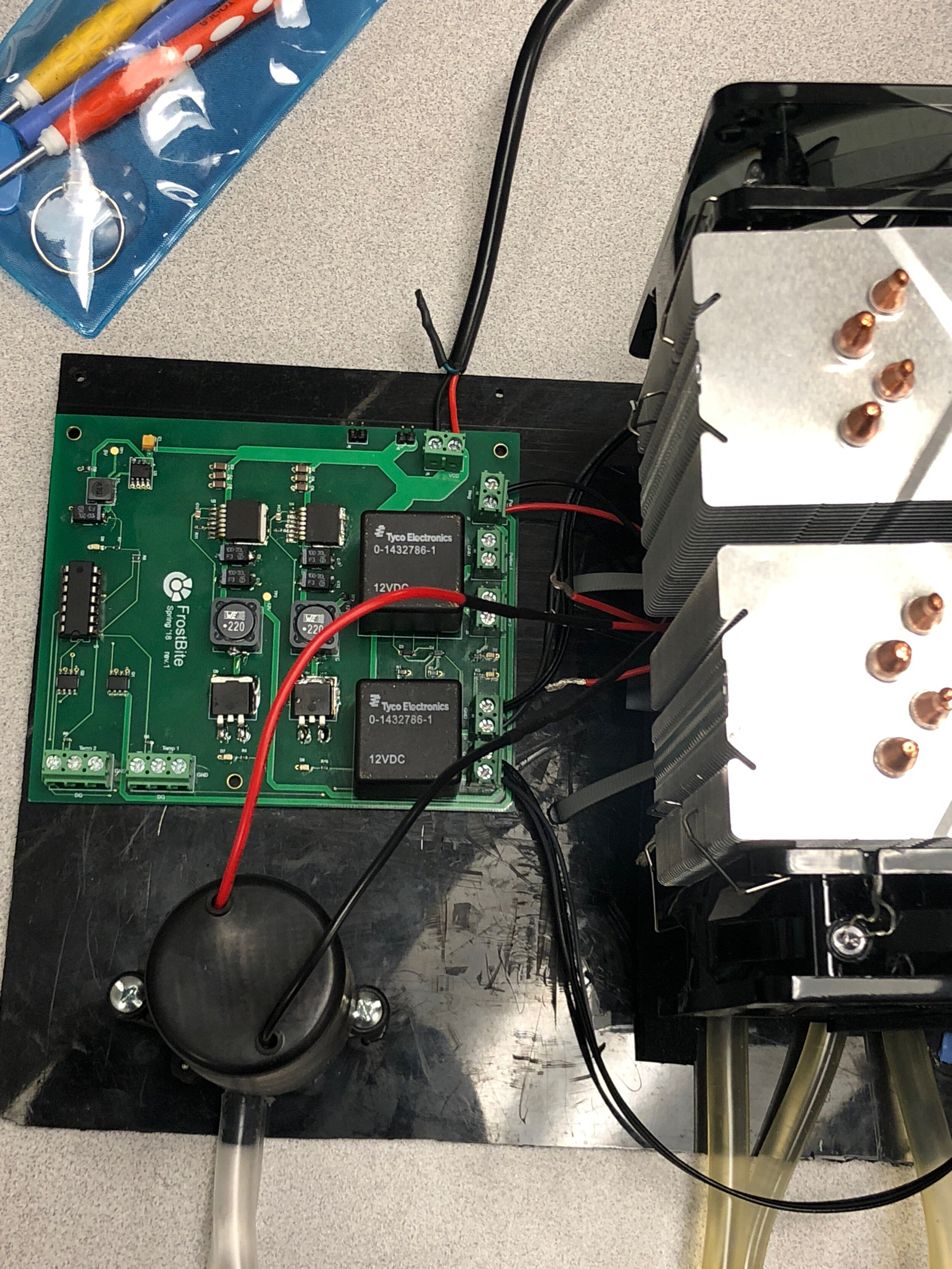
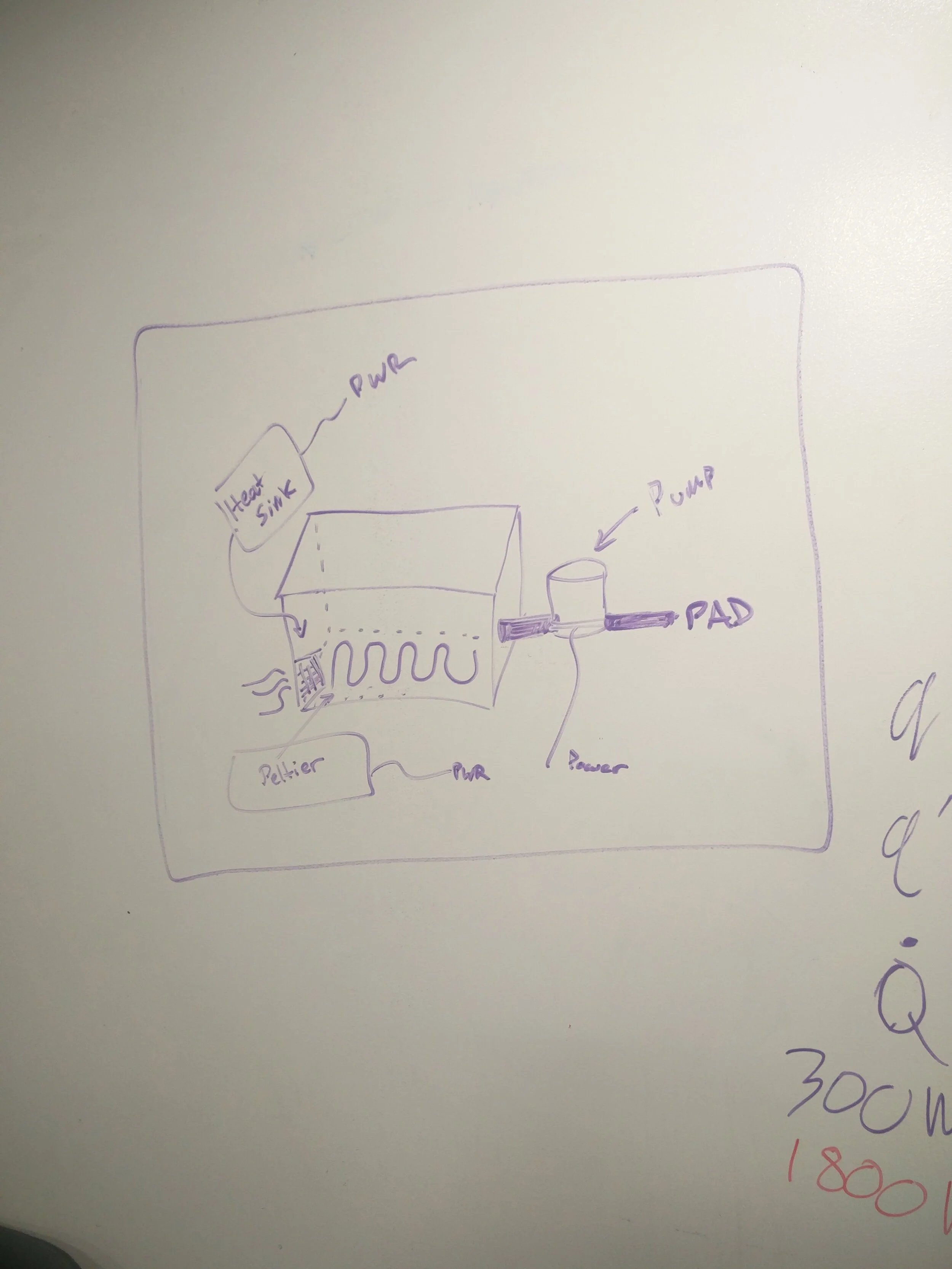